IGNITERS
Everyone associated with the hobby of high power model rocketry knows that pressing the button and having nothing happen is one of the more frustrating scenarios that happen in this sport. A good reliable igniter is pretty much a must have. Purchasing good reliable igniters is expensive so I have made my own over the years I have been in the sport.
The foundation of a good igniter is the wire used. I have been fortunate in being able to obtain a large supply of bundles of single core signal transmission wire which is ideal for making igniters. To make an igniter one needs two insulated, solid core, copper wires. Typically one uses moderatly fine gague wire, somewhere in the 24 to 30 gague size. The length depends on the length of the motor being fired.
A number of methods have and are being used for the "business end" of the igniter. Some sort of resistance bridge needs to be connected in series with one end of the pair of igniter wires which will get very hot when voltage is supplied through the igniter. A resistance between 1 and 100 ohms is typically necessary to produce a bridge temperature in a range useful in igniting a pyrogen coating which coated over the bridge. The most common bridge material is nichrome wire. I have made many igniters of this type over the years and they work well. An excellent treatise on this type of igniter can be found at the Jacobs Rocketry web site. I have moved away from this type of igniter simply because it takes a significant amount of time to make this type of igniter if one solders each end of the nichrome/copper wire bridge connection.
The type of igniter that I have come to like involves the use of a conductive carbon bridge rather than nichrome wire. One can use conductive carbon black or graphite powder as the bridge material with good success. Some people like to use 1/8 watt, 10 ohm resisters as the "bridge". I have collected quite a quantity of graphite powder through the process of machining graphite nozzles. This material works very well in my igniters.
Wire preparation
Two strands of insulated solid core copper wire of equil length are obtained and are loosly twisted (see picture below)
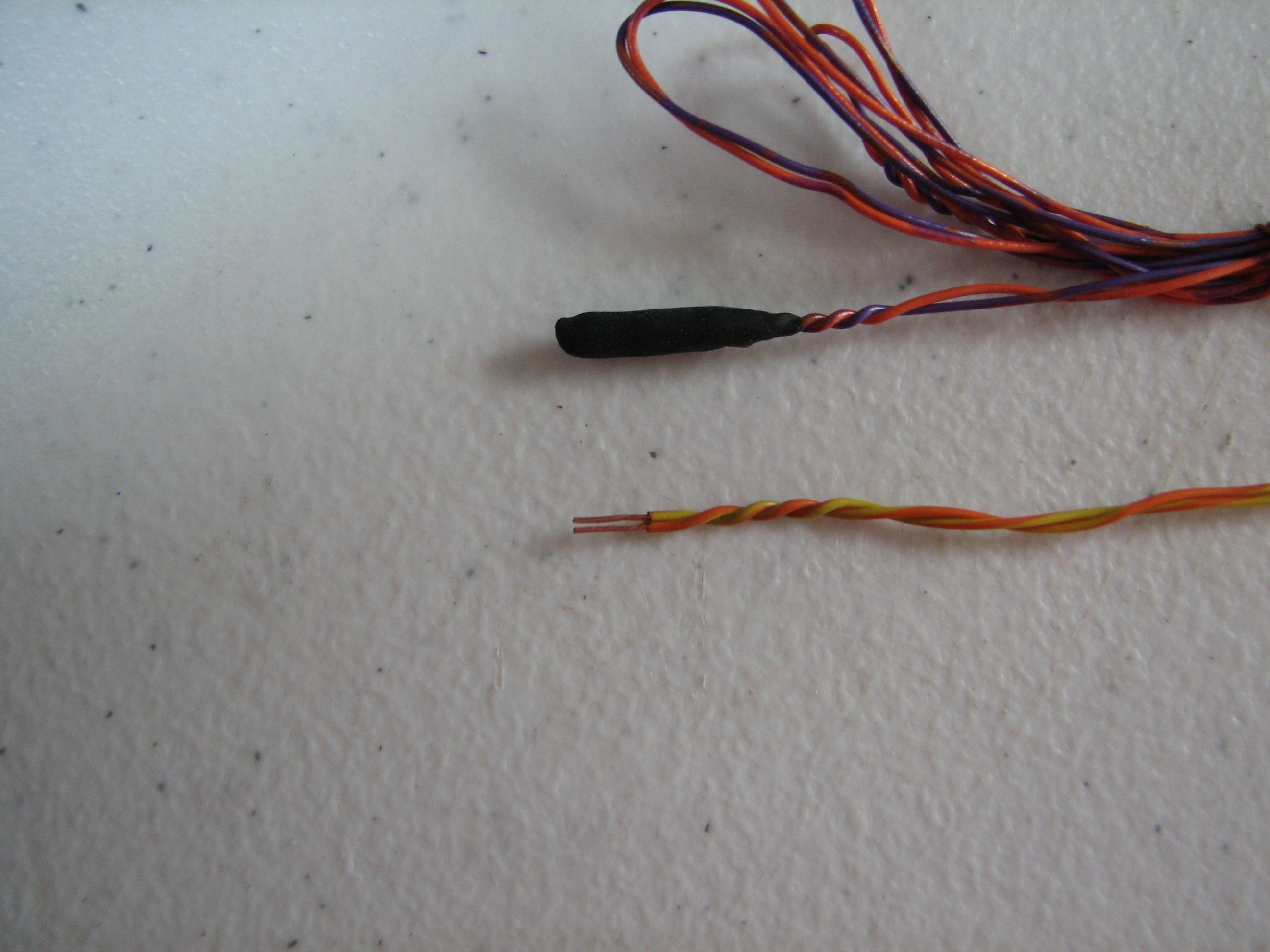
Igniter ready for dipping
Finished igniter
Both wires of one end of the pair are stripped of insulation to a length of 1/4 to 5/16 of an inch. The two wires are then twisted more securely for about an inch down from the bare ends. The two bare ends are then positioned to be parallel to one another with a spacing of about 1/64th of an inch or less. The wire is then ready to be dipped.
Bridge Coating
A solution of fine graphite powder (~ 100 to 200 micron) in nitrocellulose lacquer is prepared. The nitrocellulose lacquer can be prepared by cutting up 3 ping pong balls into small pieces and dissolving them in ~ 75 ml of acetone. Graphite powder is added to the lacquer to make a thin solution similar to a thin pancake syrup. The bridge wires ready to be coated are then dipped into the graphite soln. to a length just past the bare wires. The dipped wire is then allowed to air dry for about 30 seconds. If the bridge area shows significant indentation between the bare end wires then the wire should be dipped a second time to "round off" the dipping. The total diameter of the dipped end should be no larger than about 1/16". The dipped bridge ends should then be allowed to dry for several hours (I do the drying overnight). The resistance of several of these should be checked after drying. Resistance should be less than 50 ohms.
Pyrogen Dipping
I have used, to excellent effect, two different pyrogen formulations. All are based on KNO3 as the oxidizer. I am using formula 2 more often, the longer I use my own igniters. These formulations are listed here:
1. 8 parts KNO3
2 parts charcoal
1 part Magnalum (50 to 100 mesh)
2. 6 parts KNO3
3 parts Al dust (indian blackhead)
2 parts sulfur
The ingredients for any of these pyrogens are finely ground if necessary. The ingredients are then combined as powders and mixed well. The desired quantity (10 to 20 grams) is then placed in a small air tight vial and nitrocellulose lacquer is added slowly, with mixing, until a runny "pancake batter" consistency is reached. The graphite coated bridge wires are then dipped into the pyrogen solution to a depth of ~ 1/2 to 3/4". The resulting igniter end should increase to two to three times the diameter of the original graphite dipping. If more pyrogen, for larger motors, is desired a second dipping can be done.
The igniters should be allowed to dry overnight. Resistance usually increases somewhat. If a resistance of greater than 100 ohms is obtained this igniter should be tested to see if an igniter coated with your batch of pyrogen ignites well. I have never had an ignition problem with an igniter below 100 ohms. Above 100 ohms the igniter sometimes "pops" and does not catch on fire.
I have found this type of igniter to be very reliable. Some launch systems with higher internal resistance result in some ignition "delay" using this type of igniter. It would be best to "try one out" in your system to see how long igniter ignition takes after one "pushes the launch button".